If It’s Boeing, I Ain’t Going: The Dangers of Deregulation in a For-Profit World
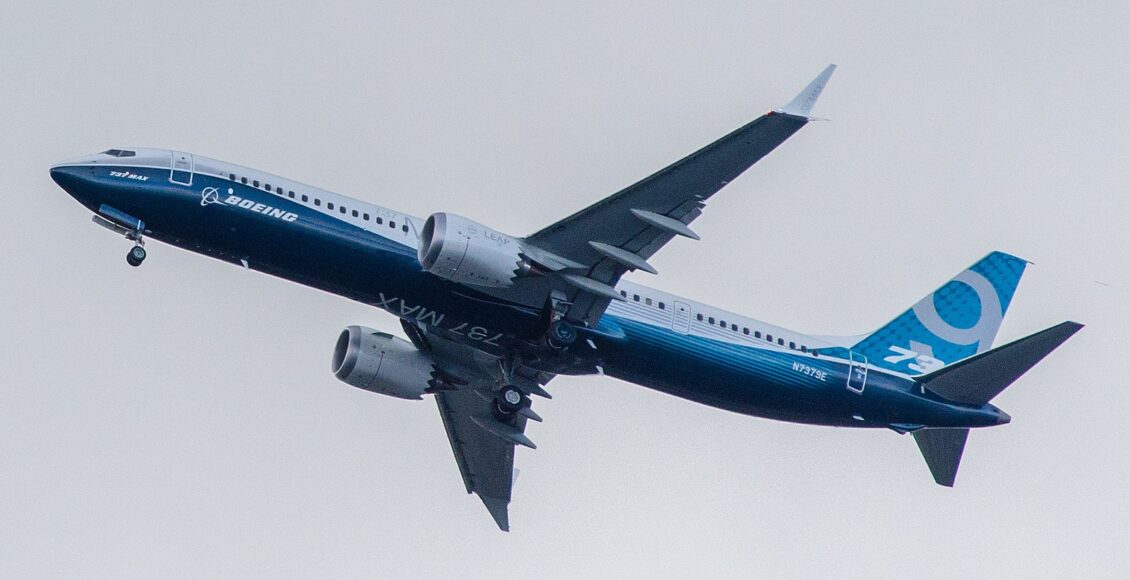
On January 5th, 2024, Alaska Airlines Flight 1282 took off from Portland International Airport. What was meant to be a routine short-haul flight to Ontario, California, quickly descended into chaos as a door plug — a panel used to replace an optional emergency exit door on Boeing’s 737 MAX 9 aircraft — violently blew off just six minutes into the journey. While the lack of casualties on the flight is nothing short of a miracle, if the incident had occurred later in the journey at a higher altitude, the explosive depressurization could have been fatal.
In the weeks following the incident, Boeing has faced considerable scrutiny from authorities. Investigations into Alaska Airlines Flight 1282 have revealed several manufacturing issues linked to the 737 MAX 9 aircraft. Missing and improperly tightened bolts caused the door plug on the two-month-old aircraft to blow off mid-flight. Regulators suspect additional problems at Boeing, as other issues like misdrilled holes and faulty engine anti-ice systems have dominated headlines.
Boeing would prefer consumers believe that the company is merely encountering a temporary hump. However, a deeper investigation reveals a more harrowing story in which lax safety standards have arisen and persisted within a company that was once celebrated globally as an icon of American engineering.
This was the scene inside the Alaska Airlines plane that made an emergency landing in Portland, Oregon, on Friday after losing a chunk of its body. Regulators have ordered U.S. airlines to stop using some Boeing 737 Max 9 planes until they are inspected. https://t.co/pWcGzL0uMF pic.twitter.com/vdDgAyA2EF
— The New York Times (@nytimes) January 6, 2024
Profit Over Innovation
Boeing’s woes and plummeting reputation are relatively recent developments for the aviation giant that has widely been recognized as the greatest innovator in aerospace history. Boeing was once so synonymous with aviation safety that pilots proudly proclaimed, “If it ain’t Boeing, I ain’t going.” However, Boeing being widely recognized as an “engineers company” did not necessarily translate into impressive stock value as costs were secondary concerns to design and quality. This changed dramatically in 1997 when Boeing successfully executed a merger with its long-standing competitor, McDonnell Douglas, for $14 billion, with a number of executives from McDonnell Douglas assuming crucial positions in Boeing’s C-suite.
Leadership quickly became driven by the expectation that Boeing would undergo restructuring to achieve significant success on Wall Street. The company began to rely on subcontractors, sold its fuselage plant to a private equity firm in 2005, and relocated its headquarters to Chicago, even though its engineers and manufacturers were based in Seattle. Today, Boeing focuses solely on the final assembly of planes, sourcing parts from other suppliers. Yet despite the cost-effectiveness and substantial boost to the company’s stock value resulting from outsourcing, engineers and manufacturers grapple with the relinquished oversight of production that has emerged. Meanwhile, in the last decade, Boeing’s leadership has spent more than $40 billion on stock buybacks — a practice in which a company repurchases its own shares to enhance stock value and shareholder returns.
Since Boeing’s merger with McDonnell Douglas, a stark transformation has occurred: company culture has shifted from being innovation-driven to prioritizing financiers on Wall Street, and in doing so, Boeing has prioritized leadership of MBAs over engineers.
The 737 MAX Program
Amidst Boeing’s shift in company culture, it faced a challenge from its fierce rival Airbus. In 2010, Airbus announced plans to update its popular plane, the A320, with a larger, more fuel-efficient engine. These design changes were minimal, facilitating pilots’ easy transition to the A320 NEO with little additional training.
Given the competitive nature of the aviation industry, any advantage in plane offerings by one company could result in substantial financial losses for the other. Boeing, recognizing this threat, decided to update its best-selling model, the 737, originally designed in the 1960s, by incorporating a larger engine. Boeing claimed that the new model, the 737 MAX, designed in MAX 7, 8, and 9 variants, closely resembled previous 737s, minimizing the need for pilot retraining. The 737 MAX quickly became Boeing’s fastest-selling plane, with airlines lining up at Boeing’s doorstep to place orders.
Unknown to the public and even aviation authorities at the time, Boeing engineers faced hurdles during the design of the 737 MAX amid challenges resulting from the company’s over-financialization. The lower positioning of Boeing’s 737 to the ground, in contrast to Airbus’s A320, necessitated elevating the position of the new, larger engine for the 737 MAX. This adjustment led to an excessive upward pitch of the aircraft during full thrust, increasing the risk of the plane stalling and free-falling from the sky.
To address this dangerous tendency to ‘pitch up,’ Boeing implemented the Maneuvering Characteristics Augmentation System (MCAS) software to push the plane downward — software that operated based on the input of a single sensor. Boeing management, concerned that disclosure could deter airlines from ordering the planes, emphasized a sense of continuity with previous models when communicating with regulatory bodies and airlines and minimized the importance of the MCAS system despite the fact that the plane was operating in a fundamentally different manner.
Boeing also encouraged a rushed production and service timeline for the 737 MAX project. Top executives, with compensation linked to company profitability and stocks, stood to gain significant benefits if the project remained on schedule, intensifying pressure on engineers to submit technical drawings and designs at double the usual pace.
The 737 MAX started commercial service in 2017, and hundreds of aircraft entered service in the following months to fulfill the enormous orders of airlines. Among the carriers was Lion Air, Indonesia’s largest.
On October 29, 2018, Lion Air Flight 610 departed from Jakarta’s bustling Soekarno-Hatta International Airport in the early morning for the nearby island of Pangkal Pinang. As the 737 MAX 8 aircraft ascended, the plane began to dive downwards, defying the pilots’ control. In a desperate struggle, the pilots fought to regain control of the aircraft. Ultimately, they were unsuccessful, and the plane hurtled into the sea just 13 minutes after takeoff — killing all 189 passengers and crew on board.
Just five months later, 157 people were killed in a similar turn of events, as Ethiopian Airlines Flight 302, also flying a 737 MAX 8 aircraft, crashed just 6 minutes after takeoff. In both tragic crashes, MCAS, which was an integral system to protect the safety of passengers on board, had malfunctioned. Pilots, unaware of its existence, grappled with the system’s unintended downward pitching, leading to the deadly loss of control over the aircraft.
Families of the 157 people who died in March’s Ethiopian Airlines crash gathered at the crash site to mark 40 days of mourning.
None of the victims' bodies were able to be recovered from the wreckage and it may take months to identify all of them. pic.twitter.com/rIvxICDygn
— AJ+ (@ajplus) April 18, 2019
The FAA’s Culpability
Following the crash of Ethiopian Airlines Flight 302 on March 10, 2019, regulators worldwide grounded the 737 MAX, including the Federal Aviation Administration (FAA). Despite being globally recognized as a standard-setter for aviation safety and the regulator of civil aviation in the United States, the FAA failed to ground the aircraft after the Lion Air crash less than five months earlier.
While Boeing publicly attributed the crashes to pilot error and inadequate maintenance, privately, after the first crash, Boeing was aware of a software issue with MCAS and had informed the FAA, albeit a month after Lion Air Flight 610 pummeled into the Java Sea. Boeing assured the FAA that a fix would be ready in a matter of weeks, leading both the FAA and Boeing to see no immediate need to ground the plane.
The FAA’s decision to not ground the 737 MAX happened in spite of the fact that the FAA’s own internal review after the Lion Air crash had concluded that without addressing the issues with MCAS, there could potentially be 15 additional crashes, resulting in thousands of deaths — a sobering statistic considering fatal crashes in aviation rarely occur under similar circumstances, let alone due to the same known single-point of failure. The FAA’s negligence in this instance was merely the tip of the iceberg in the egregious errors made by the regulatory body.
Over the past two decades leading up to the 737 MAX crashes, Boeing’s leadership consistently sought to persuade the FAA to reduce regulatory scrutiny. Additionally, owing to a shortage of government resources, support, and funding, the FAA progressively delegated more authority to Boeing for the certification of the safety of its own planes, contrary to the primary purpose of regulatory bodies, which is to ensure that companies prioritize safety and avoid shortcuts.
In the specific case of the 737 MAX, Boeing assumed the responsibility for assessing the aircraft’s safety, and decisions regarding safety regulations were made by managers prioritizing adherence to timelines rather than consulting the FAA’s technical experts. Furthermore, the FAA approved the implementation of MCAS without scrutiny and did not raise objections when Boeing omitted an explanation of MCAS from the 737 MAX’s operations manual — top FAA officials have since admitted that they did not even understand MCAS.
The door plug incident on Alaska Airlines Flight 1282 has once again subjected the FAA to intense scrutiny for its “cozy” relations with Boeing. Despite Boeing being held liable for fraud and conspiracy related to the Boeing 737 MAX 8 crashes and Boeing’s CEO David Calhoun stepping down in the aftermath of the Alaska Airlines incident, minimal action has been taken to hold the FAA accountable for its role in failing to exert its regulatory oversight.
A Cautionary Tale
What transpired at Boeing serves as a cautionary tale applicable to many companies in a for-profit world: executives can become singularly fixated on boosting profits and enhancing shareholder value. The critical lapse in the case of Boeing, turning failures into a catastrophe, was the absence of effective regulatory oversight. The Boeing case exemplifies a stark failure of self-regulation: Boeing ascended to a position where it wielded undue influence over the very regulatory agency meant to supervise it — a textbook example of regulatory capture.
While a failure to regulate companies may not lead to tragic incidents like a plane nose-diving into the ground and killing everyone on board, it is reasonable to assume that companies, regardless of the products they make, will not always be champions of consumer protection. In a corporate landscape where companies prioritize profit margins, regulatory measures are indispensable to ensure accountability and safeguard against lapses that could jeopardize public safety and well-being.
Edited by Juliet Morrison
Featured Image: “Boeing 737-9 MAX” by Jeff Hitchcock is licensed under CC BY 2.0.